摘要:如果生产的工件需要化学热处理,然后快速淬火,以获得所需的机械和冶金性能,均匀的渗层深度和硬度分布,此时,会看到一种不想要的特性:材料变形。由于在这一过程中发生的变形,制造商面临着昂贵的选择,即在热处理之前将多余的材料留在机加工工件上,只有在热处理之后,通过加工去除。当采取措施减少材料变形(在硬态加工操作之前),制造商可以显著降低成本,从而加快整个制造过程。本文将讨论对热处理和淬火工件的变形控制的独特方法,即,采用四维高压气体淬火(4D淬火下同)技术。与自由淬火或复杂的压淬方法相比,该系统具有无需夹具就能淬火单个工件的能力。4D淬火工艺使得工件以相同的方式单独淬火,并且,与淬火前相比具有最小的变形。4D淬火系统可以很容易地集成到加工中心,与传统热处理工艺相比,改善了的交货周期和成本。
2.1 液体淬火
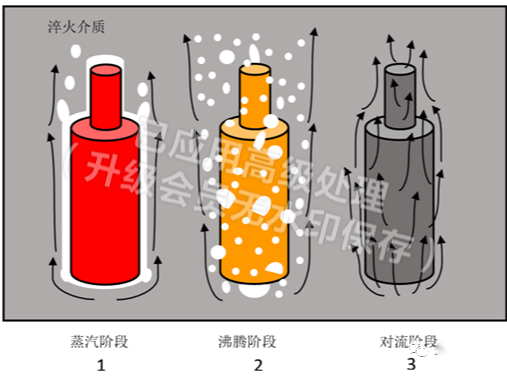
2.2 压力淬火
图2 压力淬火机的插图,©1991 ASM手册,第4卷[3]
2.3 高压气淬(HPGQ)
热处理后的高质量(干净明亮)工件
非常好的工艺重复性
环境友好
无IGO
最大限度地降低淬火变形
热加工过程的完全自动化
易于工艺设置
全SCADA系统
炉子多工艺的灵活性
紧凑设计
图3 安装好的卧式真空炉
图4卧式真空炉气流模型
3 批量淬火
图5典型的批量摆放
图6 批量与单件的二维冷却气体流动图
图7 工件在20bar的N2从上向下气流淬火6s后的温度梯度
4 4D高压气体淬火
4.1 4D淬火
4D淬火是一种新的工艺,可以显著改善淬火工艺,主要集中在减少变形和使工艺具有可重复性。减少变形主要是通过在淬火/卸载室中安装高压气淬系统来实现的(图8)。4D淬火平台采用专有的冷却歧管和腔室布置(图8),在淬火过程中包围着工件。这种方法确保了冷却气体在工件几何形状(顶部、底部和侧面)上的均匀流动。当谈到顶部、底部和侧面淬火时,称之为“3D”冷却。
图8 4D淬火/卸载室
为了实现淬火时的第4维,工件被放置在淬火室,专有的冷却歧管围绕着工件,最后支撑台旋转工件,而冷却氮气流遍工件。我们将三维淬火与零件旋转相结合,缔造了4D淬火,能够进一步提高淬火均匀性。采用4D HPQG,它可以得到最好的有可能的淬火均匀性。此外,最重要的是,由于冷却喷嘴可以调整以适应工件的精确尺寸和几何形状,所以淬火可充分优化,变形显著减小。
图9 4D淬火室中的淬火气体流动
4.2 4D淬火能力
当讨论淬火时,加热炉系统将采用各种淬火工艺/介质,以达到所需的冶金性能。基于材料硬化的能力,或者我应该说“无能”被硬化,为达到工件最终使用所需要的硬度,可能需要用更强烈的冷却速度。淬火图(图10)显示了批量淬火过程中采用的三种主要类型的淬火油(快、中、慢)与各种淬火气体(N2、He、H2)的关系。我们首先看淬火油,三种油的一般传热系数(或淬火能力)范围大约为1000 - 2500(W/m2K)。
后面,图表显示了这三种气体之间的关系,以及当室内压力增加时它们的表现。垂直的虚线代表真空HPGQ炉两类通常构造。14bar标记处的虚线代表典型的单室批次HPGQ炉,24bar标记处的虚线代表典型的多室批次HPGQ炉。简单来说,多室意味着有一个专用的加热室和淬火室,其中加热区不淬火,因此多室HPGQ炉的性能比单室炉更好。然而,多室HPGQ炉的一个缺点是比单室炉制造更复杂、成本更高。
当比较N2批次HPGQ炉与油淬炉时,虽然N2是HPGQ中最常用的气淬介质,但只有进入20-24 Bar范围时,它才开始变得像油一样强。He和H2比其他两种气体性能都要好。然而,缺点是He的购买成本非常高,需要昂贵的回收系统,而H2有其固有的安全法规和顾虑,使其不能用于当今的淬火工艺。那我们该怎么办?正如你所看到的,当只使用9 Bar的N2淬火气体时,4D淬火的能力属于快油淬火范围。
图10 4D淬火、批次HPGQ和油淬火速度关系
4.3 4D淬火优化
在4D淬火室内的淬火过程的优化可以通过调整其一个或多个特性等多种方式进行(表1)。对这些参数的简单调整,用户现在有完全的灵活性,以优化淬火工艺、减少变形,保持零件到零件的重复性,并在工件热处理后实现精密的精度。
表1 4D淬火特性
特性 | 描述 |
淬火压力 | 1-10bar绝对气压 |
气体流速 | 冷却风机转速控制 |
气体歧管 | 淬火气体在零件周围分布均匀 |
支撑台旋转 | 开/关,转速与方向调整 |
支撑台摆动 | 角度调整 |
气流随时间变化 | 可论秒控制 |
4.4 均匀淬火
为了进一步说明4D淬火的均匀淬火能力,系统可以通过淬火室上的小型摄像机记录整个淬火过程。从视频(图11)的快照中可以看到,淬火非常均匀且迅速。在这个例子中,工件在15秒内从845℃的“红热”颜色冷却到425℃的黑色。所有这些特性都可以调整,这意味着4D淬火材料冷却系统是一个完美的工具,为冷却过程的形成和控制提供了无限的可能性,允许用户设定淬火工件所需的最佳参数。
图11 4D淬火实时淬火图片
5 案例
联轴器套筒是传动系统的关键工件(图12)。由于其复杂的几何形状,它们在热处理过程中容易产生较大的几何变形。联轴器套筒变形的几个原因是它的薄壁结构和轮齿的几何形状。
图12联轴器套筒试验工件照片
在下面的案例研究中,20个套筒在SECO/WARWICK单片流UniCase Master真空炉中进行低压渗碳和4D淬火(图13),然后进行回火处理。为了证明4D淬火在热处理后能减少工件变形,采用三坐标(CMM)对工件进行尺寸测量。测量精度为2µm。热处理前尺寸测量记为“未加工件(green part)”,在热处理后记为“表层硬化件(case hardened)”。为进一步增强说服力,测量了几个不相关的关键尺寸,包括:径向跳动、轴向跳动、总节距偏差、总齿廓偏差和总螺旋线偏差等(图14.1-14.5)。
图13 UniCase Master 完全热处理系统
图14.1 径向跳动测量结果
图14.2 轴向跳动测量结果
图14.3 总节距偏差Fp测量结果
图14.4 总齿廓偏差Fa测量结果
图14.5 总螺旋线偏差Fb测量结果
在这个试验的结论中,你可以看到,套筒在热处理前后的几何形状变化极小。大多数尺寸特征与热处理前的差异小于0.001英寸(0.025mm)。在4D淬火试验中,套筒的AGMA质量等级达到了>12级,证明了该系统优于任何其他淬火方法。
从这个角度看,在其它典型的批量热处理过程中,相同的套筒可能会产生0.020-0.030英寸(0.5到0.75mm)的尺寸偏差,这使得制造商面临两难选择:是花费更多的时间和成本来消除这些巨大的偏差呢,还是将工件全部报废?
当前和最佳的硬化过程解决方案,不管是批量的还是连续的,都不能满足当前和未来的高产量齿轮和其他高产量产品在质量、可重复性、灵活性、生产一体化、环境友好以及成本等方面的要求,主要因为工件是成批处理的。
4D淬火系统是一种真正的单件流式真空淬火系统,消除了现有技术方案的缺点。满足当前和未来大批量齿轮制造商的要求,具有以下特点:
处理结果的精度重现
4D淬火减少淬火变形
能集成到连续生产线
精益制造
为齿轮和轴承制造商以及其他行业实现高产量生产力
设计灵活,可微调工艺参数和生产量
监控生产,100%可追溯性和单个工件的报告
不用夹具(成本,能源)和批量材料搬运物流
不用淬火油、清洗机、清洗液,
安全可控,避免潜在的火灾和爆炸危险
清洁工艺,对环境没有影响
应用HPGQ前沿技术
4D淬火可以显著改善淬火过程,特别是减少变形。该系统的性能和优势将硬化工艺提升到一个新的水平,并可以为大批量齿轮和轴承制造商日益严格的质量和生产要求的发展铺平道路。
如果您对我们感兴趣,请登录网站http://www.xtjhrcl.com